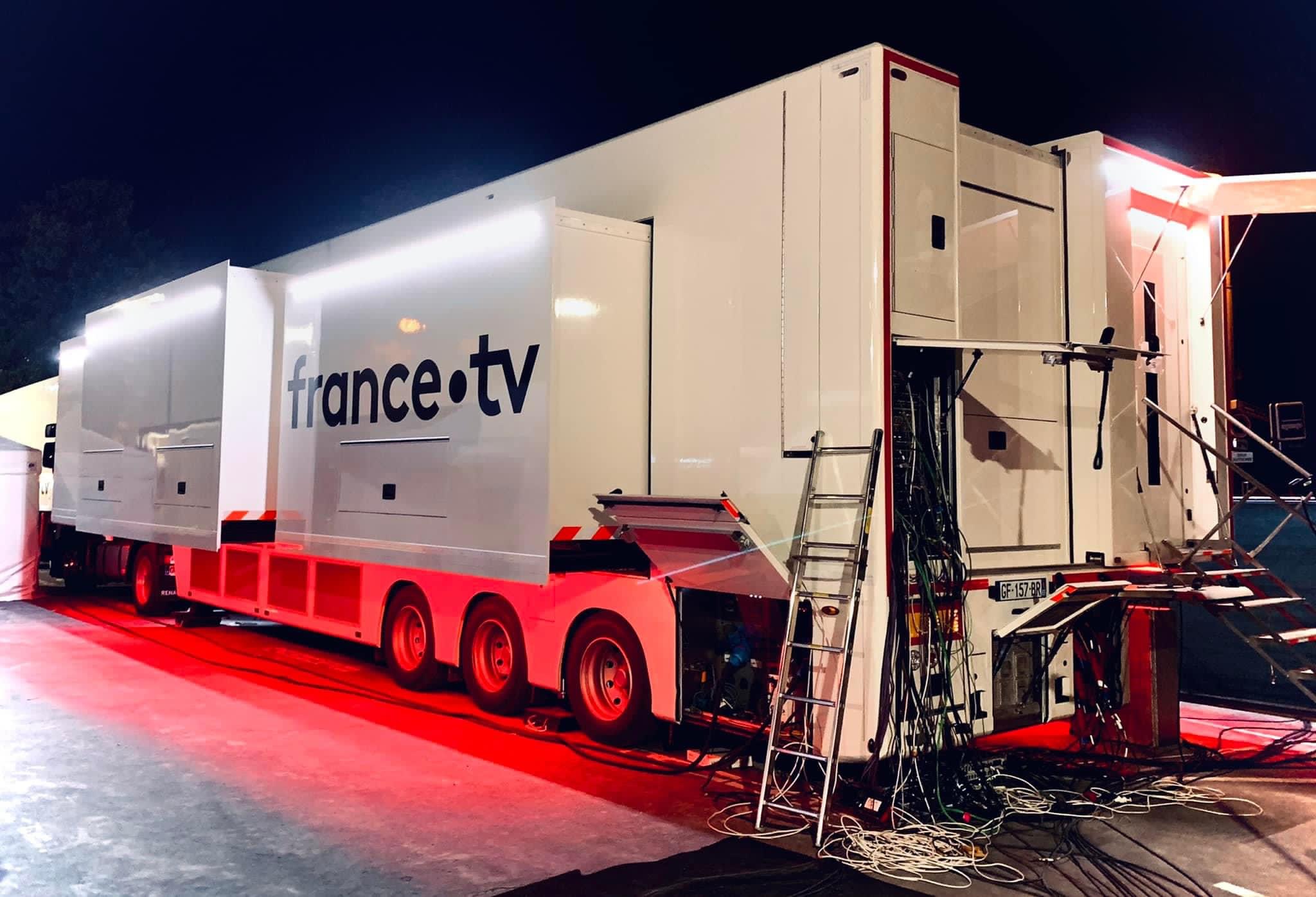
France Télévisions recently put into operation its new production OB truck, the UM1. Based on a hybrid SDI/IP architecture, it provides UHD and HDR images thanks to a capacity of 25 cameras and two video control rooms working simultaneously. It operates in two configurations, with its four open extensions accommodating 36 workstations or in semi-closed mode with a more limited capacity of 24 workstations.
Translated from an article by Pierre-Antoine Taufour.
The new France Télévisions truck, named UM1 (for Mobile Unit 1) replaces one of the trucks in the fleet, inaugurated in 2004. After 18 years of existence, it had reached the end of its life, both technologically and layout speaking.
Laurent Vindevoghel, project coordinator at La Fabrique de France Télévisions explains the origin of this project: “Rather than manufacturing two identical trucks, it was decided to acquire a range of more agile and therefore more varied vehicles, meeting all the needs of France Télévisions, ranging from coverage of events requiring great technical power such as the Tour de France, to more modest productions with very strong constraints, including environmental ones.
This is why the UM1, flagship of this new fleet of vehicles, is capable of meeting all production demands with an exceptional capacity to accommodate both technical and production workstations or to receive guests.
It will be supplemented by a second truck, the UM2, with smaller reception capacities. However, equipped with substantial technical resources, it will be able to be used in even more restricted spaces or in cities with tighter streets.
A third mobile production equipment, the UM3, will complete this fleet in the first half of 2023 in the form of a mobile control room in flight cases. These three means will be able to interconnect in order to offer an unprecedented strike force for exceptional operations; we are obviously thinking of the 2024 Olympic Games.
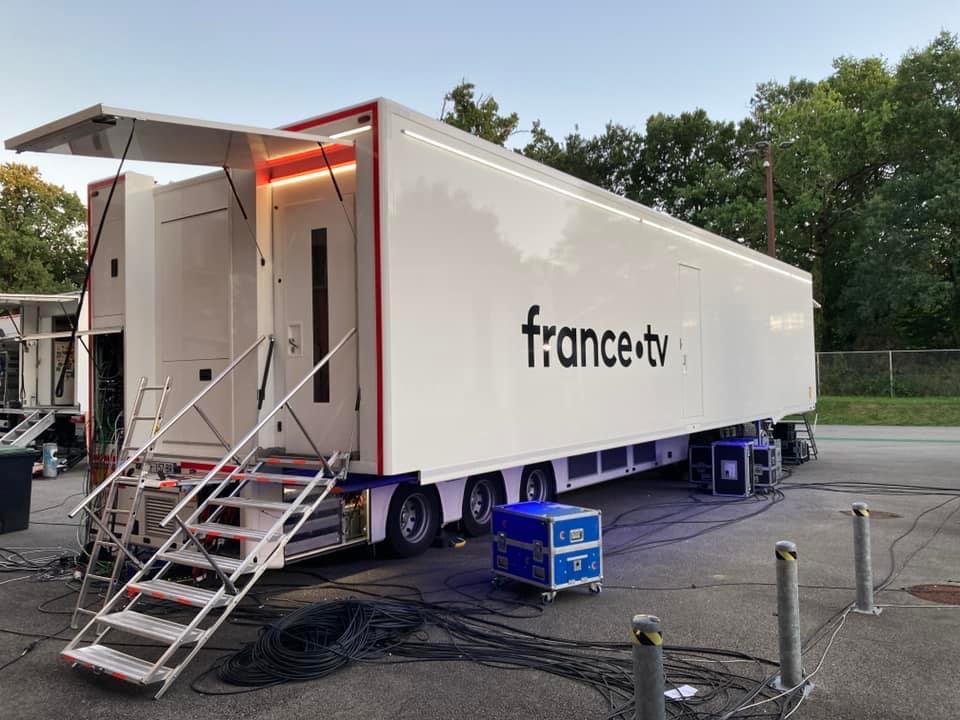
The project is co-managed by the Engineering and Process Support division of the Technology and Information Systems Department (DTSI) and La Fabrique de France Télévisions, which brings together the group’s production resources. The first studies were launched in 2019 with the drafting of specifications and then a consultation with integrators.
BCE (with its subsidiary BCE France) was selected and began the detailed studies in close collaboration with the two entities of France Télévisions in charge of the project. Unfortunately, this phase coincided with the Covid epidemic and forced the teams to work remotely during multiple videoconferences. All the validation of the 3D plans was done on telework.
The new UM1 truck is built on a semi-trailer chassis. The manufacture of the body lasted a full year, followed by a six-month integration and configuration phase. This new UM1 OB van was put into operation during the summer of 2022, with the broadcast of the French National Day concert from the Eiffel Tower, the European Athletics Championships coverage taking place in Munich, to name but a few, providing 243 hours of live broadcast on the France 2 and France 3 television channels.
A hybrid SDI/IP architecture
The choices for the technical architecture of this new OB van were the subject of long brainstorming sessions and multiple exchanges between the department in charge of Engineering and Support Process and the production teams of La Fabrique.
When the project was launched in 2019, IP technologies did not seem mature enough, in particular in terms of equipment connectivity, and the first feedbacks regarding all IP vans were not completely conclusive.
The hypothesis of a full IP van was therefore not retained by the team in charge of the project. But, given the lifespan of such equipment, it did not seem appropriate to design it exclusively in SDI either.
Laurent Vindevoghel details the choices made: “For the new UM1 truck, we have chosen a hybrid SDI/IP architecture. All the audio part is in IP with a Calrec Apollo console. The video equipment is connected in SDI but has been chosen in such a way that it may evolve towards full IP. Third important element, a Riedel MediorNet network is deployed in optical fiber with a TDM transport according to a mesh topology and can also easily migrate to IP.
The MediorNet network will also be used in the future to interconnect the three mobile units for the coverage of a major event. The IP infrastructure is organized around a Cisco Nexus 9300 network core according to a Fabric-type architecture in spine and leaf mode, sized to accommodate video equipment when it will evolve towards all-IP.”
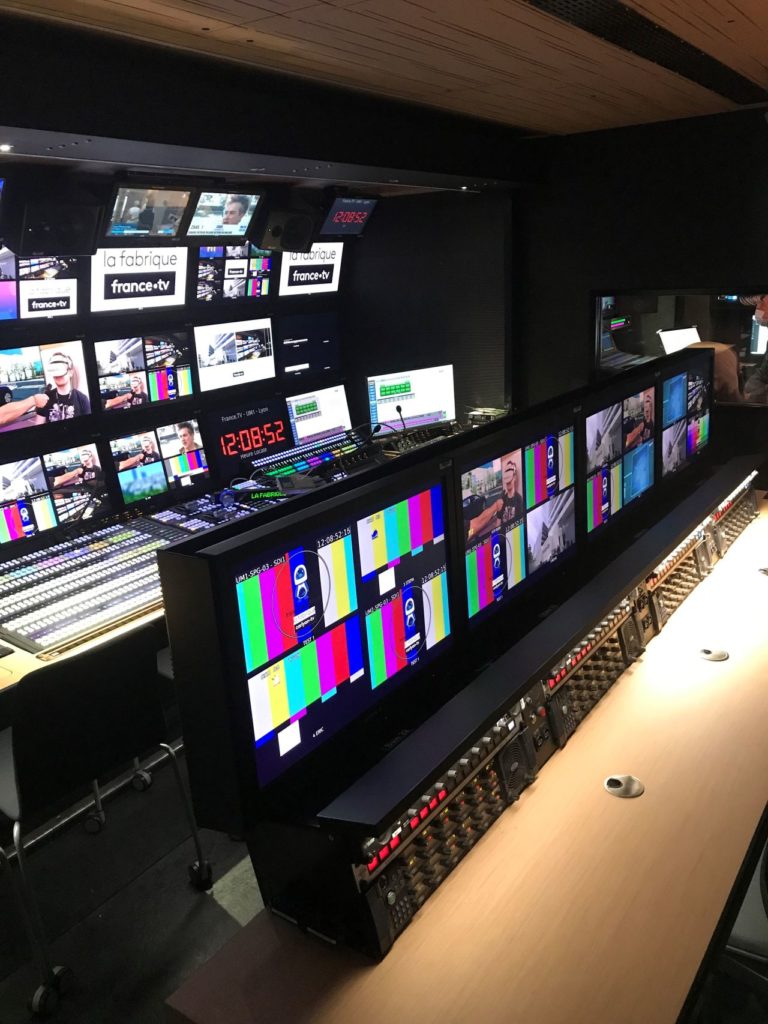
UHD and HDR video equipment
All video equipment in the control room is designed to operate in HD and UHD, with a HDR dynamics option. They are sized for a capacity of 25 cameras. To date, the new truck is equipped with Sony HDC 3500 rental cameras.
The main video control room is supplied with a Sony XVS 9000 video mixer with a console with four mix/effect bars. Its resources can be shared with a second independent control room, equipped with a more modest console with two mix/effects. The objective is to be able to produce two distinct programs in two separate control rooms with two production teams.
The classic example is the coverage of a major international sporting event with the main control room supplying the international signal, in UHD for example, while the secondary control room provides appropriate packaging for a national channel with an HD or UHD start. It is even possible to provide a third output for a local channel or an IP streaming or compatible ST-2110 with a simplified implementation on a switch bar. For external sources, the OB vehicle is capable of receiving and processing HD, UHD and IP signals (streaming or ST-2110).
To avoid colorimetric differences in the display of images, the models of monitors fitted to screen walls and workstations have been limited to three references. Sony PVM-X2400 (or PVM-X1800 for the audio control room) UHD/HDR reference monitors equip the vision engineer stations and the screens (preview and final) of the two video control rooms. All other workstations are equipped with Sony LMD-A240 monitors. The display of images in multiview mode is ensured via MediorNet MicronN UHD frames equipped with the corresponding application.
The audio control room is organized around the Calrec Apollo audio mixer operating in full IP (SMPTE ST-2110 and AES67). The associated desk is equipped with 72 faders and can be configured to provide three separate mixes corresponding to the sounds of the three video programs that the OB vehicle can produce simultaneously. A second Calrec Type R modular mixer is installed to serve as a backup to the main system. It also works with any IP. The choice of all IP facilitates the transfer of sources from the main mixer to the backup.
The audio control room is designed to ensure multi-channel mixing and therefore has 5.1 sound experience in the cabin. The sound system is made up of a set of Quested brand active loudspeakers, consisting of the SR7 model, associated with SBR10 subwoofers and completed with V2108 proximity loudspeakers. Beforehand, the modulations are processed by a Trinnov processor to optimize the rendering of the loudspeakers and refine the spatialization of the sound. An identical 5.1 sound system is set up in the main video control room. In the case of a production of several simultaneous live broadcasts, the audio mixing of each of them will be done in stereo and each sound engineer will monitor his mix through headphones.
A multitude of IP networks and a virtualized computer
As indicated at the beginning of the article, the entire sound recording and audio mixing system is based on an IP infrastructure compatible with SMPTE ST-2110 and AES67 whose core network is a Cisco Nexus 9300 with fabric architecture in spine and leaf mode. But it should not be thought that this is the only IP network operated in the UM1. Without establishing an exhaustive list, we can quote the broadcast controller provided by the Lawo VSM tool, an IP KVM matrix, the Clear-Com intercom system associated with its FreeSpeak wireless system, the INs and OUTs of IP streams, the control of equipment such as cameras on turrets…
To pass all these data flows smoothly and without malfunction, it was necessary to carry out an extensive research with BCE and the IT Security Department of France Télévisions to build the network as a whole, define a multitude of VLANs and configure the active equipment at the spine and leaf switches. On many productions, a private optical fiber is brought to the filming location in order to provide access to all the computer resources of the headquarters. This connection also offers supervision tools to technical teams to provide assistance in case of a problem.
When no access to the fiber network is available on site, the OB van can still connect, with limited functionalities, via 4G and 5G gateways.
On the IT side, part of the resources necessary for its operation have been clustered on a server farm running with Nutanix, a hyperconverged infrastructure solution. Each computer and server are installed there in the form of a virtual machine.
In the UM1 truck, around twenty machines are grouped together on three 1U rack servers. The memory and processor resources of each virtual machine are dynamically reallocated according to the needs and the functions to be provided. This solution also ensures operational reliability because if one of the servers goes down, the tasks assigned to it are dynamically reallocated to the other two. However, this innovation brings complexity and feedback will be used to improve the solution on the UM2.
The addition of all these networks and these virtual machines leads the designers of the van to take into account all the issues related to cybersecurity. Care must be taken to properly isolate each activity and reliably separate each component of the network. Last minute external machines or content via USB keys are no longer an option. Strict procedures are now in place changing work habits.
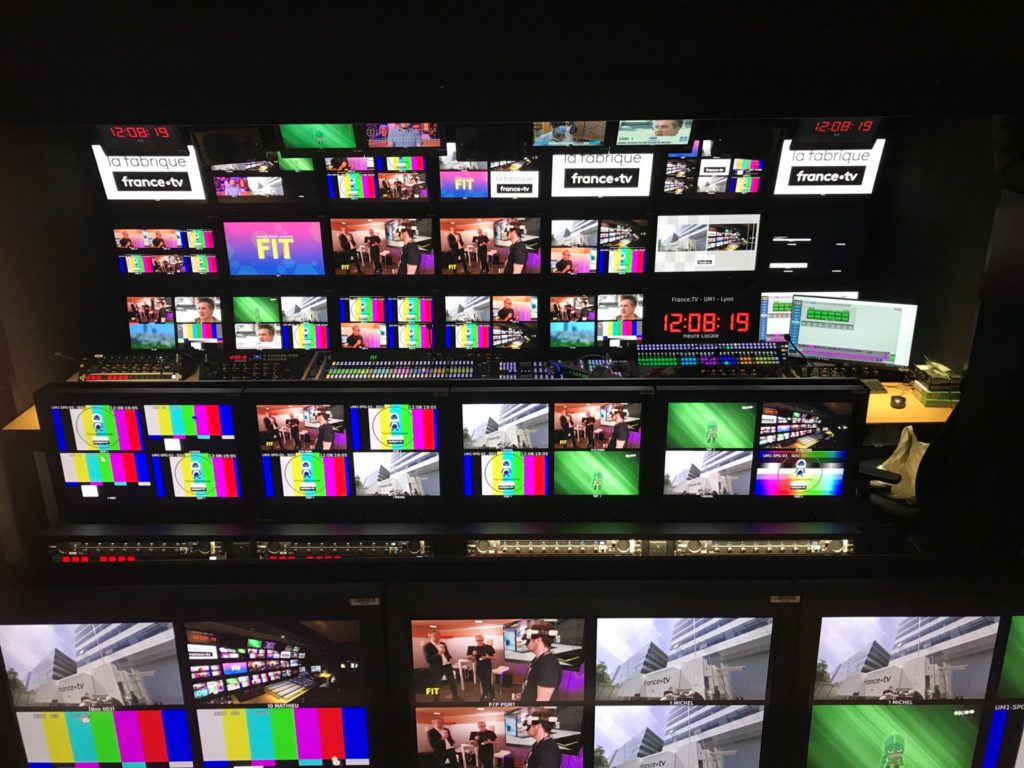
“You no longer connect additional equipment in the same way as before. You must declare it and open the right ports and use the protocols provided. We need real security access,” comments Laurent Vindevoghel. “At the end of the construction of the van, a real cybersecurity audit was also carried out with attack and penetration tests on the various networks that serve it.”
Spacious and modular layouts
When visiting the OB van, the terms comfort, space, modularity and inventiveness immediately come to mind.
Laurent Vindevoghel explains that “when drafting the specifications, we included a certain number of requirements in terms of layouts and operating methods. In particular the possibility of using the van in two configurations, with all the extensions open or semi-closed to limit its space on the ground. This gave the BCE teams a lot of trouble.”
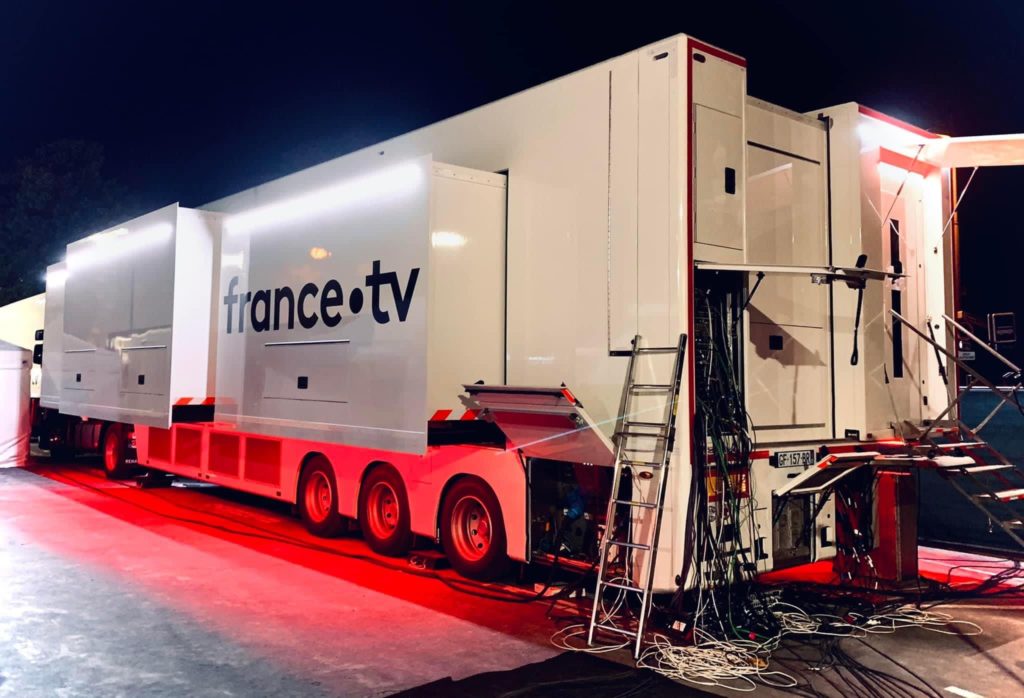
“To provide a large, comfortable workspace for a production team of 36 people, it was essential to extend the central volume of the coach with extensions on both sides,” emphasizes Mikaël Graignic of BCE France. “On the left side, three volumes extend outwards: a first for the sound control room mixing console and its screens, a second for the main control room image wall and a third for the secondary control room. On the right side of the truck, an extension has been fitted along its entire length, but unlike the classic assembly similar to a drawer that fits into a piece of furniture, this one completely covers the structure of the central box of the trailer.”
This totally innovative configuration (a first in France according to Philippe Mauduit, President of BCE France) offers several advantages, on the one hand there is a larger interior volume compared to the classic drawer system and on the other hand there is the possibility of making a continuous and uniform floor, without steps when passing from one volume to another thanks to a drop-down floor system.
The interior fittings and the layout of the equipment have been studied so that the van can operate either in a totally open configuration with all the extensions deployed, giving a capacity of 36 workstations, or work only with straight extension out, a good way to limit floor space. In this case, the secondary video control room is no longer accessible (the console of the video mixer and its work plan fold up vertically thanks to a flap).
The volumes of the main video control room and the sound control room are reduced, but the installation of their respective desks on sliding furniture makes it possible to preserve working comfort. In this semi-open configuration, the number of workstations in the truck is limited to 24.
This dual mode of operation, totally open or half-closed, has led to the resolution of multiple mechanical problems. One of the main concerns was the position of the video and sound mixing consoles as well as their distance from the screen walls. The console of the main video control room was mounted on a sliding piece of furniture allowing it to be placed in the optimum working position. As a direct consequence of the two ways of opening extensions in production, the volumes of the main control room and the sound control room are variable, and it is therefore essential to modify the number and layout of workstations associated with them.
Production stations adjustable in position and height
The most spectacular layout is probably the one of the production stations usually located behind the director. In the fully open position, two rows of four production stations are available. These so-called universal workstations can accommodate production or editing workstations, slow-motion workstations, synth operators and VIP guests.
To offer maximum comfort but also all the flexibility depending on the mode of operation of the van, each row of four stations is mounted on a rail to be closer to the mixing console or away from it. In the semi-closed position, this serves to bring the two rows closer together by eliminating the intermediate space between the seats and leaving only one row in operation. The two tables of the four universal workstations are mounted on a vertical motorization system which makes it possible to adjust the working height of the operators, either seated on a chair, or on a high stool or even standing.
To allow all these movements, in depth and in height, the connection cables to the equipment of the production stations arrive from the ceiling and run on cable carriers. Each production station is permanently equipped with its 24-inch monitor but can receive a second removable monitor to be fixed above the first, as needed.
The secondary video control room, which can only be used in the totally open configuration, accommodates six workstations, two facing the mixer desk and four other universal workstations. This second control room is placed in continuity with the cabinet of the main control room but can be completely isolated from the latter thanks to an insulating glass partition. It has dedicated access, independent of the main control room, if the two production teams wish to work completely independently.
A third cell is fitted out to accommodate the five vision engineer stations and five so-called universal stations and intended more for slow-motion, recording and playout operators. It is also in this cell that the van manager, Jean-Luc Martin, is located.
Laurent Vindevoghel explains: “We fostered flexibility in the organization of production, and this is why it is so important to have this notion of universal workstations. Except for the vision engineers, the workstations are not assigned to a specific trade. Depending on the needs, work habits, or even desires of each person, an operator can choose to work in a quieter environment such as the secondary control room even if it is not operated or on the contrary near the director in the main control room. Slow-motion operators can also work on an editing station in the recording cell.”
An efficient audio cabin
The audio control room is fitted at the front of the control room at the level of the connecting arm of the trailer. The mixer console can be used with the audio control room extension open or closed. Three seats take place in front of the main mixer desk to use the three sound mixing stations as explained above. For recordings of classical music concerts or festivals, a workstation has been set up for the MMO (Musician director on waves) who assists the sound engineer.
At the rear of the sound control room, there is an independent room assigned to the management of the intercoms which also serves as an access to the sound cabin. In a logic of maximising operations flexibility, the separating partition of this intercom room with the sound control room is sliding and is transparent but comes with good sound insulation. Thus the team of sound engineers can decide to isolate the intercom station as during sports broadcasts which can be quite agitated on this aspect or on the contrary to group the two cells into one.
The development of a sound booth is always a challenge because it must offer a very good level of performance in a very restrictive environment while preserving its ergonomics: reduced dimensions, noise pollution from neighboring spaces, external disturbances, air treatment which can be noisy and all this in a structure with many moving parts, which are difficult to seal at the joints.
The result obtained in the UM1 van lives up to expectations and when you enter the sound control room, you immediately feel the calm and the high level of isolation. During our visit, there was a heavy downpour, and someone remarked, “You can’t even hear the rain! “.
Recently, the UM1 truck was used to ensure the live transmission of an opera to cinemas. During the rehearsals the team in charge of the sound recording was able to observe that the acoustic rendering on site in the room was identical to that obtained in the sound booth of the van.
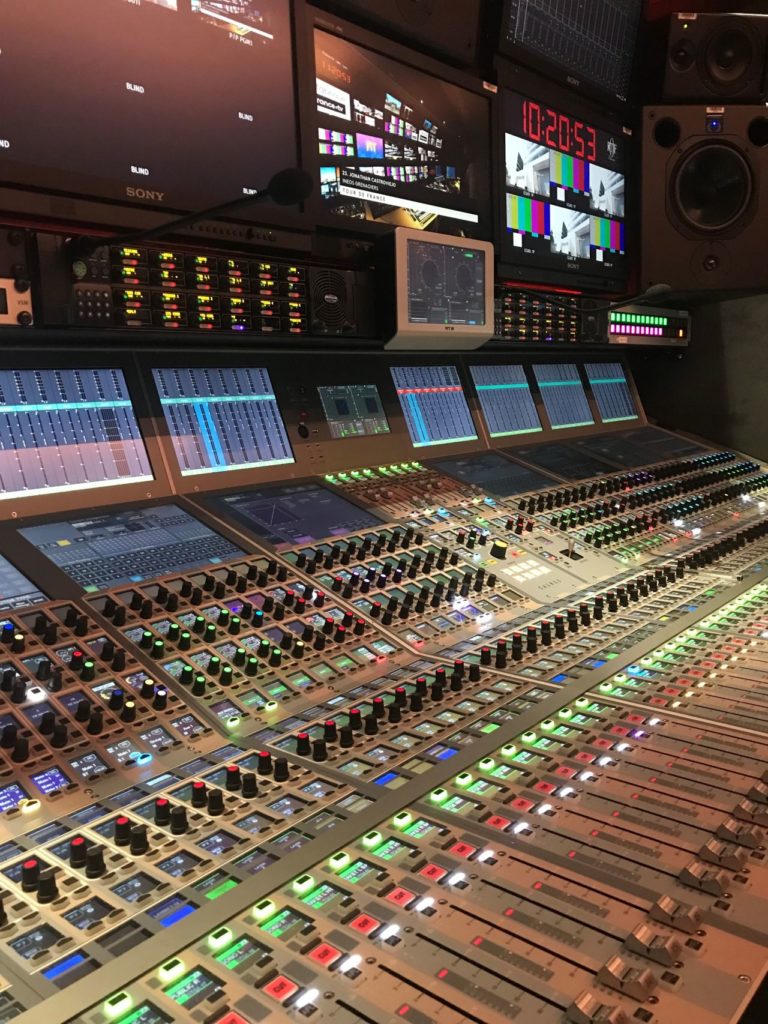
François-Xavier Ballon, sound engineer, explains that “the UM1 coach is used for very diverse performances: sports, game shows, variety shows, operas, classical music concerts. Each situation is relevant to different acoustic renderings. The layout of the cabin, its sound system and its acoustics must be adjusted to these different types of programme. And to this is added an additional constraint, the variable dimensions of the cabin and the position of the mixing desk depending on whether the extension is extended or not.”
An innovative air change system
During the year and on its various trips, the OB van will encounter highly variable climatic conditions. It is therefore necessary to equip it with heating and air conditioning systems. Beyond the thermal aspect, with a technical team of around thirty people, air renewal is essential. A forced ventilation system was installed to diffuse clean air in the various technical cells.
Schematically, this device works like a residential VMC but upside down. It draws in fresh air from the outside, which is cooled or heated depending on the temperature and which is diffused into the various control rooms.
This system is equipped with a filtering device to eliminate pollen, bad smells and even fine particles such as those carrying Covid. Thus, the van will be able to continue to be operational at full capacity even in the event of a new pandemic. According to the truck design team, this device would be a first in France and perhaps in Europe.